Cómo diseñar piezas de plástico
Breve descripción:
A diseñar piezas de plásticoes definir la forma, el tamaño y la precisión de las piezas, en función del papel que juegan las piezas en el producto y la regla del proceso de moldeo del plástico. El resultado final son dibujos para la fabricación del molde y la pieza de plástico.
La fabricación de productos comienza con el diseño. El diseño de piezas de plástico determina directamente la realización de la estructura interna, el costo y la función del producto, y también determina el siguiente paso de la producción de moldes, el costo y el ciclo, así como el proceso y el costo de moldeo por inyección y posprocesamiento.
Las piezas de plástico se utilizan ampliamente en diversos productos, instalaciones y vidas de las personas en la sociedad moderna. Las piezas de plástico requieren diferentes formas y funciones. Utilizan materiales plásticos y sus propiedades son variadas. Al mismo tiempo, hay muchas formas de fabricar piezas de plástico en la industria. Por tanto, diseñar piezas de plástico no es un trabajo sencillo.
Diferentes diseños de piezas y materiales se producen en diferentes procesos. El procesamiento para moldear plástico incluye principalmente a continuación:
1.moldeo por inyección
2.moldeo por soplado
3.moldeo a presión
4.moldeo rotacional
5.termoformado
6.extrusión
7.fabricación
8.espuma
Existen numerosas formas de producirlos en masa. El moldeo por inyección es un método de fabricación popular, debido a que las piezas de plástico moldeadas por inyección al 50% ~ 60% se producen mediante moldeo por inyección, es una capacidad de producción de alta velocidad.
Vitrina para algunas piezas de plástico que diseñamos:
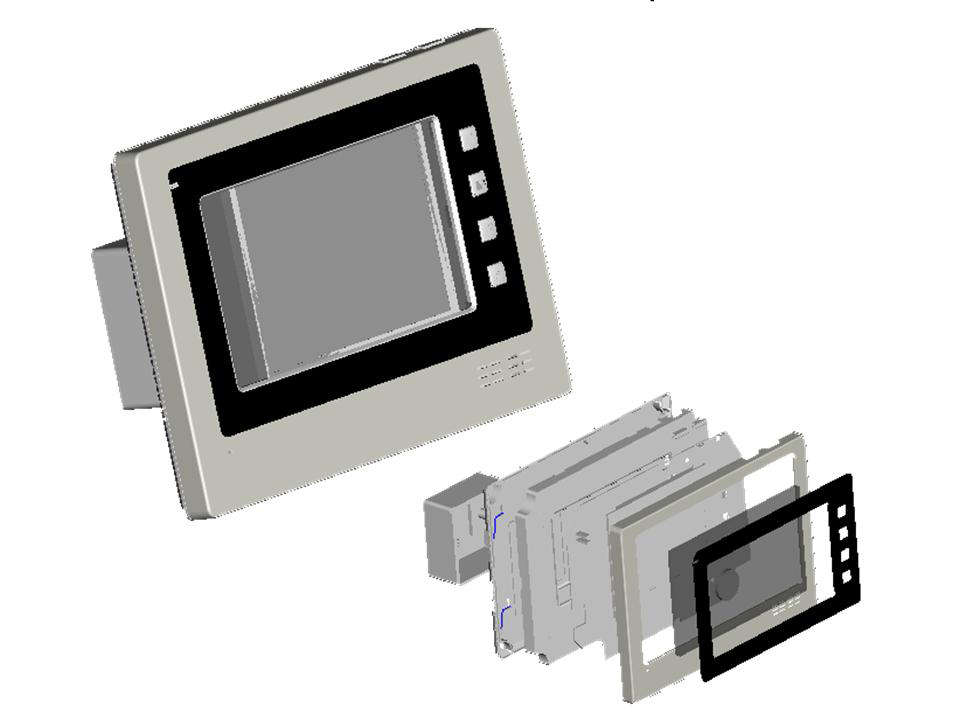
Caja de plástico del teléfono de visión
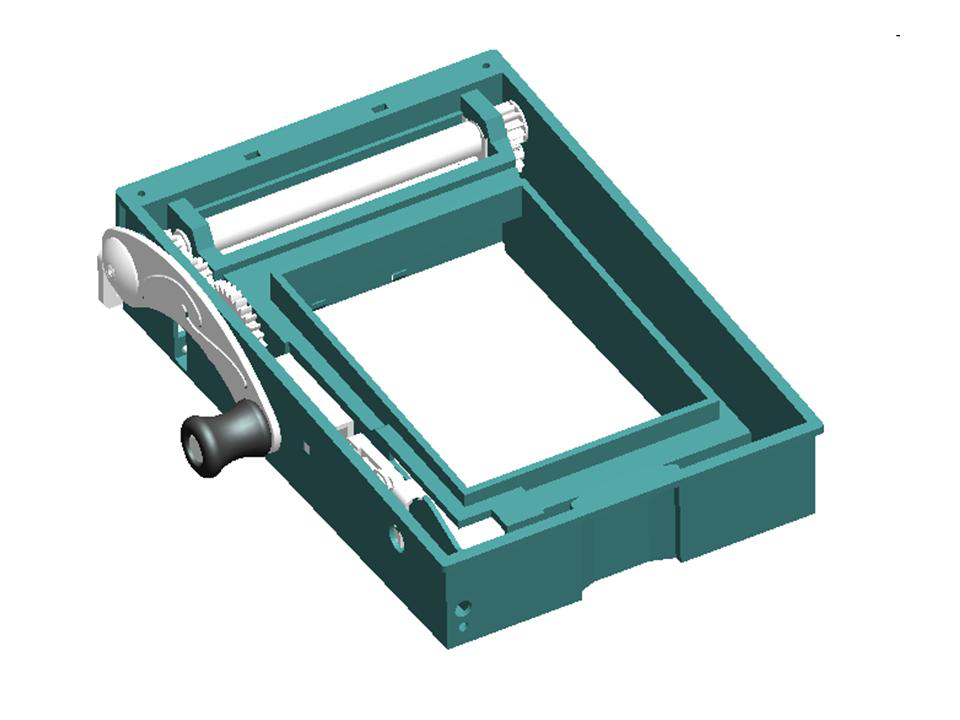
Partes de plástico del mecanismo
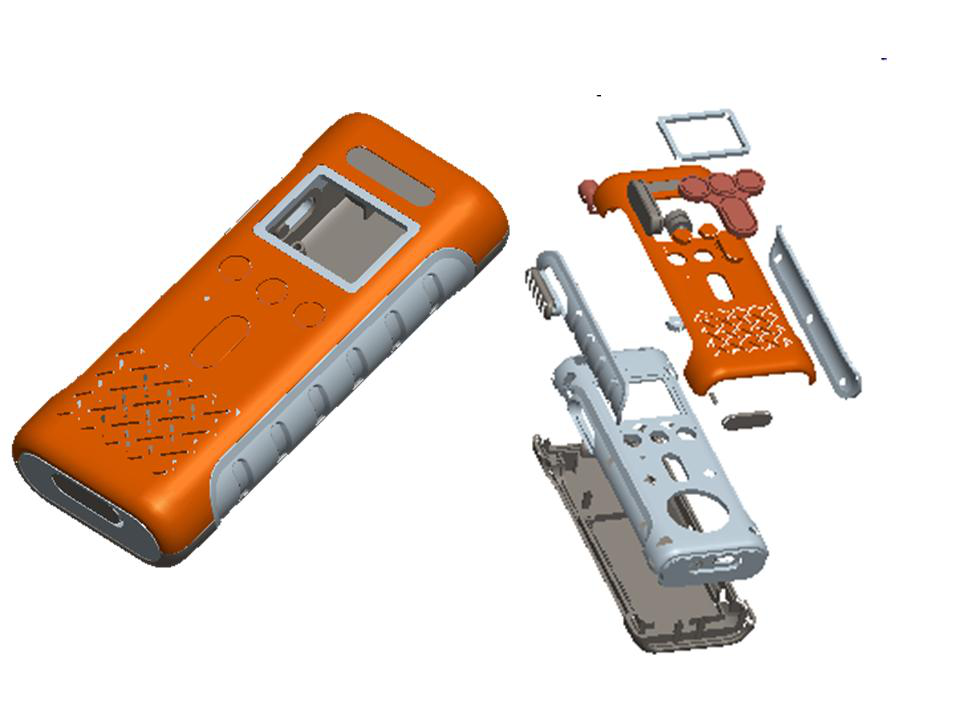
Cajas de plástico de electrónica
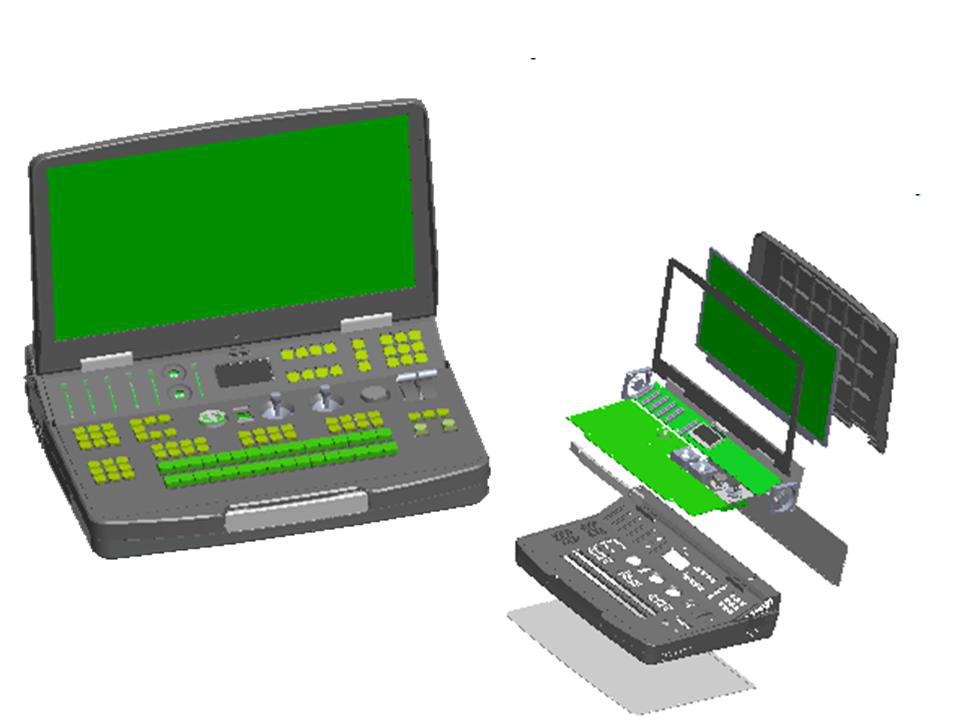
Carcasa de plástico para instrumento
A continuación compartimos en detalle cómo diseñar piezas de plástico en tres aspectos.
* 10 consejos para diseñar piezas de plástico que debes conocer
1.Determina el diseño de apariencia y el tamaño del producto.
Este es el primer paso en todo el proceso de diseño. De acuerdo con la investigación de mercado y los requisitos del cliente, determine la apariencia y función de los productos y formule tareas de desarrollo de productos.
De acuerdo con la tarea de desarrollo, el equipo de desarrollo lleva a cabo el análisis de viabilidad técnica y tecnológica del producto y construye el modelo de apariencia 3D del producto. Luego, de acuerdo con la realización de la función y el montaje del producto, se planifican las posibles piezas.
2.Separe las piezas individuales de los dibujos del producto, elija el tipo de resina plástica para las piezas de plástico
Este paso consiste en separar las piezas del modelo 3D obtenido en el paso anterior y diseñarlas individualmente. De acuerdo con los requisitos funcionales de las piezas, elija materias primas plásticas o materiales de hardware adecuados. Por ejemplo, el ABS se utiliza normalmente en
Se requiere que la carcasa, ABS / BC o PC tenga ciertas propiedades mecánicas, partes transparentes como pantalla, poste de luz PMMA o PC, engranajes o piezas de desgaste POM o Nylon.
Después de seleccionar el material de las piezas, se puede iniciar el diseño de detalle.
3.Definir ángulos de desmoldeo
Los ángulos de tiro permiten quitar el plástico del molde. Sin ángulos de tiro, la pieza ofrecería una resistencia significativa debido a la fricción durante la extracción. Los ángulos de tiro deben estar presentes en el interior y el exterior de la pieza. Cuanto más profunda sea la pieza, mayor será el ángulo de desmoldeo. Una simple regla general es tener un ángulo de desmoldeo de 1 grado por pulgada. No tener suficiente ángulo de desmoldeo puede resultar en raspaduras a lo largo de los lados de la pieza y / o grandes marcas de clavijas de expulsión (más sobre esto más adelante).
Ángulos de inclinación de la superficie exterior: cuanto más profunda sea la pieza, mayor será el ángulo de inclinación. Una simple regla general es tener un ángulo de desmoldeo de 1 grado por pulgada. No tener suficiente ángulo de desmoldeo puede resultar en raspaduras a lo largo de los lados de la pieza y / o grandes marcas de clavijas de expulsión (más sobre esto más adelante).
Por lo general, para que la superficie se vea bien, la textura se hace en la superficie de las piezas. La pared con textura es rugosa, la fricción es grande y no es fácil sacarla de la cavidad, por lo que requiere un ángulo de dibujo más grande. La textura más gruesa es el ángulo de dibujo más grande necesario.
4.Definir espesor de pared / espesor uniforme
El moldeo de forma sólida no se desea en el moldeo por inyección debido a las siguientes razones:
1). El tiempo de enfriamiento es proporcional al cuadrado del espesor de la pared. Un tiempo de enfriamiento prolongado para el sólido derrotará la economía de la producción en masa. (mal conductor del calor)
2) .La sección más gruesa se contrae más que la sección más delgada, por lo que introduce una contracción diferencial que da como resultado una deformación o una marca de hundimiento, etc. (características de contracción de los plásticos y características de pvT)
Por lo tanto, tenemos una regla básica para el diseño de piezas de plástico; en la medida de lo posible, el espesor de la pared debe ser uniforme o constante en toda la pieza. Este espesor de pared se denomina espesor de pared nominal.
Si hay alguna sección sólida en la pieza, debe hacerse hueca introduciendo un núcleo. Esto debería garantizar un espesor de pared uniforme alrededor del núcleo.
3) ¿Cuáles son las consideraciones para decidir el espesor de la pared?
Debe ser lo suficientemente grueso y rígido para el trabajo. El espesor de la pared puede ser de 0,5 a 5 mm.
También debe ser lo suficientemente delgado para enfriarse más rápido, lo que resulta en un menor peso de la pieza y una mayor productividad.
Cualquier variación en el espesor de la pared debe mantenerse lo más mínima posible.
Una pieza de plástico con diferentes espesores de pared experimentará diferentes velocidades de enfriamiento y diferente contracción. En tal caso, lograr una tolerancia cercana se vuelve muy difícil y muchas veces imposible. Cuando la variación del espesor de la pared sea esencial, la transición entre los dos debe ser gradual.
5.Diseño de conexión entre piezas
Por lo general, necesitamos conectar dos carcasas. Formar un espacio cerrado entre ellos para colocar los componentes internos (conjunto o mecanismo de PCB).
Los tipos habituales de conexión:
1). Mosquetones:
La conexión de mosquetones se usa comúnmente en productos de tamaño pequeño y mediano. Su característica es que los ganchos de seguridad generalmente se colocan en el borde de las piezas y el tamaño del producto se puede hacer más pequeño. Una vez ensamblado, se cierra directamente sin utilizar herramientas como destornillador, troquel de soldadura por ultrasonidos y otros. La desventaja es que los mosquetones pueden hacer que el moho sea más complicado. El mecanismo deslizante y el mecanismo elevador son necesarios para realizar la conexión de los ganchos de seguridad y aumentar el costo del molde.
2). Uniones roscadas:
Las uniones roscadas son firmes y fiables. En particular, la fijación tornillo + tuerca es muy fiable y duradera, permitiendo múltiples desmontajes sin fisuras. La conexión por tornillo es adecuada para productos con gran fuerza de bloqueo y desmontaje múltiple. La desventaja es que la columna de tornillos ocupa más espacio.
3). Jefes de montaje:
La conexión de los salientes de montaje es para fijar dos partes mediante la estrecha coordinación entre los salientes y los agujeros. Esta forma de conexión no es lo suficientemente fuerte para permitir desmontar productos. La desventaja es que la fuerza de bloqueo disminuirá a medida que aumenta el tiempo de desmontaje.
4). Soldadura ultrasónica:
La soldadura ultrasónica consiste en colocar las dos partes en el molde ultrasónico y fusionar la superficie de contacto bajo la acción de la máquina de soldadura ultrasónica. El tamaño del producto puede ser más pequeño, el molde de inyección es relativamente simple y la conexión es firme. La desventaja es el uso de molde ultrasónico y máquina de soldadura ultrasónica, el tamaño del producto no puede ser demasiado grande. Después del desmontaje, las piezas ultrasónicas no se pueden volver a utilizar.
6 socavados
Los cortes son elementos que interfieren con la eliminación de cualquier mitad del molde. Los cortes pueden aparecer en casi cualquier lugar del diseño. Estos son tan inaceptables, si no peores, que la falta de un ángulo de inclinación en la pieza. Sin embargo, algunos cortes son necesarios y / o inevitables. En esos casos, necesario
los cortes se producen deslizando / moviendo partes en el molde.
Tenga en cuenta que crear cortes es más costoso cuando se produce el molde y debe mantenerse al mínimo.
7.Soporte de costillas / fuelles
Las nervaduras en la pieza plástica mejoran la rigidez (relación entre carga y deflexión de la pieza) de la pieza y aumentan la rigidez. También mejora la capacidad de moldeado ya que acelera el flujo de masa fundida en la dirección de la nervadura.
Las nervaduras se colocan en la dirección de máxima tensión y deflexión en superficies sin apariencia de la pieza. El llenado, la contracción y la expulsión del molde también deberían influir en las decisiones de colocación de las costillas.
Las costillas que no se unen con la pared vertical no deben terminar abruptamente. La transición gradual a la pared nominal debería reducir el riesgo de concentración de esfuerzos.
Costilla - dimensiones
Las costillas deben tener las siguientes dimensiones.
El grosor de la nervadura debe estar entre 0,5 y 0,6 veces el grosor nominal de la pared para evitar marcas de hundimiento.
La altura de la nervadura debe ser de 2,5 a 3 veces el espesor nominal de la pared.
La costilla debe tener un ángulo de tiro de 0,5 a 1,5 grados para facilitar la expulsión.
La base de la nervadura debe tener un radio de 0,25 a 0,4 veces el espesor de pared nominal.
La distancia entre dos nervios debe ser de 2 a 3 veces (o más) el espesor de pared nominal.
8 bordes redondeados
Cuando dos superficies se encuentran, forma una esquina. En la esquina, el grosor de la pared aumenta a 1,4 veces el grosor nominal de la pared. Esto da como resultado una contracción diferencial y una tensión de moldeado y un tiempo de enfriamiento más prolongado. Por lo tanto, el riesgo de falla en el servicio aumenta en las esquinas cerradas.
Para resolver este problema, las esquinas deben suavizarse con radio. El radio debe proporcionarse tanto externa como internamente. Nunca tenga una esquina interna afilada ya que promueve el agrietamiento. El radio debe ser tal que confirme la regla de espesor de pared constante. Es preferible tener un radio de 0,6 a 0,75 veces el espesor de la pared en las esquinas. Nunca tenga una esquina interna afilada ya que promueve el agrietamiento.
9.Diseño de jefe de tornillo
Siempre usamos tornillos para fijar dos medias cajas juntas, o sujetar PCBA u otros componentes en las piezas de plástico. Por lo tanto, los salientes roscados son la estructura para atornillar y piezas fijas.
El saliente del tornillo es de forma cilíndrica. El jefe puede estar vinculado en la base con la parte madre o puede estar vinculado a un lado. La unión lateral puede resultar en una sección gruesa de plástico, lo cual no es deseable ya que puede causar marcas de hundimiento y aumentar el tiempo de enfriamiento. Este problema se puede resolver uniendo el saliente a través de una nervadura a la pared lateral como se muestra en el croquis. El saliente se puede hacer rígido proporcionando nervaduras de contrafuerte.
El tornillo se usa en el jefe para sujetar alguna otra parte. Hay tornillos que forman roscas y tornillos que cortan la banda de rodadura. Los tornillos para roscar se utilizan en termoplásticos y los tornillos para cortar roscas se utilizan en piezas plásticas termoestables inelásticas.
Los tornillos formadores de roscas producen roscas hembra en la pared interna del saliente por flujo frío: el plástico se deforma localmente en lugar de cortarse.
El saliente del tornillo debe tener las dimensiones adecuadas para soportar las fuerzas de inserción del tornillo y la carga colocada sobre el tornillo en servicio.
El tamaño del orificio en relación con el tornillo es fundamental para la resistencia al desgarro de la rosca y la extracción del tornillo.
El diámetro exterior del saliente debe ser lo suficientemente grande para soportar las tensiones del aro debido a la formación de la rosca.
El orificio tiene un diámetro ligeramente mayor en el hueco de entrada para un tramo corto. Esto ayuda a ubicar el tornillo antes de introducirlo. También reduce las tensiones en el extremo abierto del saliente.
Los fabricantes de polímeros dan pautas para determinar la dimensión del jefe de sus materiales. Los fabricantes de tornillos también dan pautas para el tamaño correcto del diámetro interior del tornillo.
Se debe tener cuidado para asegurar uniones soldadas fuertes alrededor del orificio del tornillo en el saliente.
Se debe tener cuidado para evitar el estrés moldeado en el jefe, ya que puede fallar en un entorno agresivo.
El diámetro interior del saliente debe ser más profundo que la profundidad de la rosca.
10.Decoración de superficie
A veces, para obtener una apariencia atractiva, a menudo hacemos un tratamiento especial en la superficie de la caja de plástico.
Tales como: textura, alto brillo, pintura en aerosol, grabado láser, estampado en caliente, galvanoplastia, etc. Es necesario tener en cuenta en el diseño del producto con anticipación, para evitar que el procesamiento posterior no se pueda lograr o cambios de tamaño que afecten al ensamblaje del producto.